Exactly How Routine Packaging Equipment Service Can Minimize Downtime Expenses
Exactly How Routine Packaging Equipment Service Can Minimize Downtime Expenses
Blog Article
Professional Packaging Devices Service for Seamless Operations
In today's fast-paced production environments, the significance of professional packaging equipment solution can not be underrated. Such solutions not just improve operational efficiency but additionally play a crucial duty in decreasing downtime and making certain item high quality. By leveraging competent specialists for preventive maintenance and punctual repair services, services can navigate the intricacies of equipment administration (packaging equipment service). Nevertheless, the landscape of tools solution is developing, presenting both obstacles and chances that require more exploration. What factors should organizations consider when investing in these crucial services to safeguard their competitive side?
Importance of Specialist Service
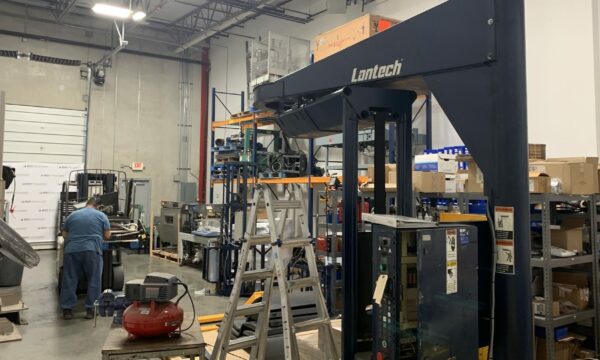
Moreover, normal maintenance by professionals assists extend the life-span of packaging equipment. Professional solution carriers are equipped with extensive understanding of different equipment kinds and sector standards, allowing them to carry out preventative maintenance efficiently. This positive technique not just lowers the chance of unforeseen break downs but likewise enhances overall operational reliability.
In addition, skilled service can considerably contribute to compliance with governing criteria. Product packaging devices must follow rigorous security and high quality guidelines, and specialist specialists guarantee that these standards are fulfilled constantly. This not only safeguards product honesty but also shields the business's credibility.
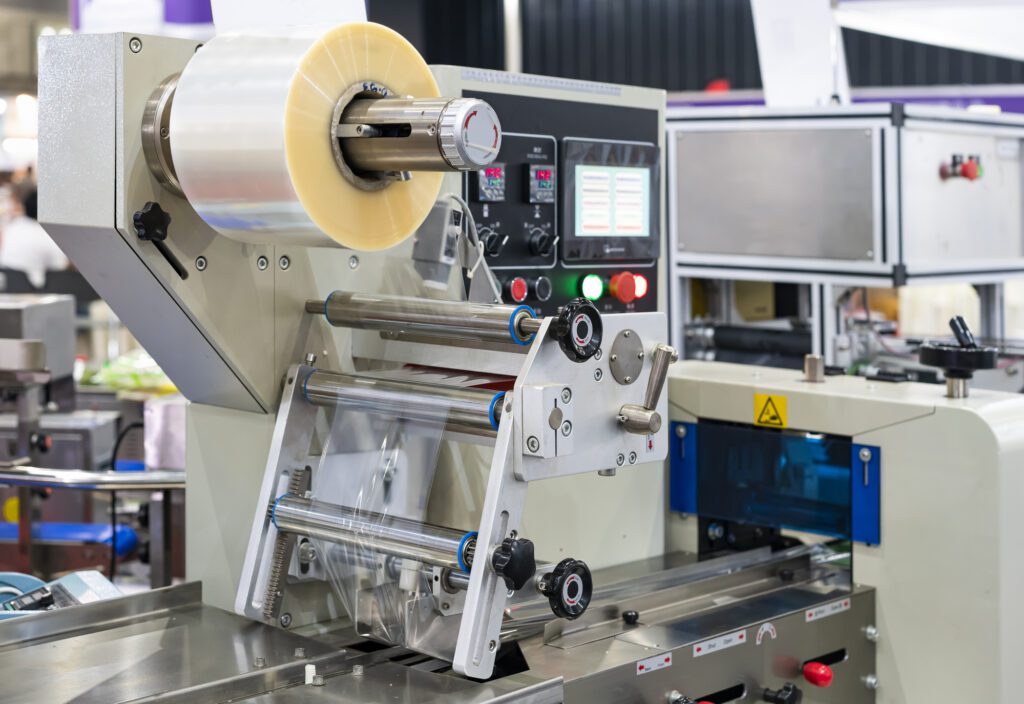
Advantages of Expert Support
Involving expert support for product packaging devices not only enhances functional effectiveness but additionally provides a variety of additional advantages that can considerably impact an organization's bottom line. One of one of the most noteworthy benefits is the minimization of downtime. Expert professionals can swiftly diagnose and resolve problems, ensuring that manufacturing lines stay energetic and decreasing the financial losses related to still equipment.
Additionally, expert support frequently includes preventative upkeep, which can extend the life expectancy of product packaging devices. By regularly servicing machinery, potential troubles can be recognized and attended to before they escalate into expensive fixings or replacements. This positive approach not only conserves money however additionally enhances item quality by making certain that devices operates within optimum criteria.
Additionally, leveraging the know-how of seasoned professionals can cause boosted conformity with market guidelines. These specialists remain updated on the most recent criteria and can guide companies in carrying out ideal practices, thus preventing possible lawful liabilities.
Types of Product Packaging Equipment Provider
When it involves product packaging equipment services, companies can pick from a selection of alternatives customized to meet their specific needs. These services normally fall under numerous categories, each developed to boost functional performance and decrease downtime.
Preventative upkeep services focus on regular evaluations and maintenance jobs to make certain that devices operates smoothly and reduces the likelihood of unanticipated break downs. This proactive method can extend the life-span of equipment and improve performance.
Repair solutions are vital for attending to devices malfunctions or failings - packaging equipment service. Knowledgeable professionals identify the issues and perform essential repair services, guaranteeing that the equipment is brought back to ideal working problems promptly
Installment services are crucial when presenting new product packaging equipment. Professionals deal with the setup, guaranteeing that the machinery is incorporated properly right into existing lines and functions as planned.
Training solutions offer team with the required abilities and understanding to run devices successfully. This training can cover whatever from standard operation to innovative troubleshooting.
Lastly, getting in touch with solutions provide critical insights right into optimizing packaging procedures, helping services identify areas for renovation and execute ideal practices. In general, picking the right combination of these solutions can significantly improve product packaging procedures.
Key Functions to Look For
What important qualities should companies think about when choosing packaging equipment solutions? Furthermore, the schedule of comprehensive support solutions, consisting of setup, upkeep, and troubleshooting, makes certain that companies can count on prompt support when problems occur.
Another key attribute is the versatility of solution offerings. A company that can adapt to click over here progressing organization requirements, such as modifications in production quantity or product packaging specs, will certainly be important in maintaining performance. Technology assimilation ought to be a top priority; contemporary product packaging tools solutions must integrate sophisticated technologies, such as automation and real-time tracking, to enhance performance.
Lastly, track record and customer comments should not be overlooked. Involving with endorsements and instance research studies can give a clearer image of a provider's reliability and high quality. By taking into consideration these important attributes, businesses can make enlightened choices that will support their product packaging operations and add to total success.
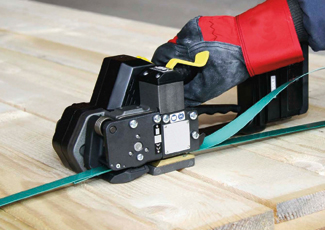
Purchasing Long-Term Success
Buying long-lasting success in product packaging equipment solutions requires a calculated strategy that my company prioritizes sustainability and scalability. Companies must focus on choose devices that not only meets existing operational needs yet likewise suits future growth and technological improvements. This insight minimizes disruptions and improves total performance.
A crucial element of this financial investment is the normal maintenance and service of equipment. Establishing a positive service routine minimizes downtime and expands the life-span of equipment, ultimately resulting in cost financial savings. Partnering with expert company ensures that the tools is optimized for performance, thus keeping high manufacturing criteria.
In addition, incorporating cutting-edge modern technologies, such as automation and IoT connection, can dramatically boost functional capacities. These improvements enable for real-time surveillance and data evaluation, More about the author allowing business to make informed choices that straighten with their long-term goals.
Last but not least, purchasing staff member training on new innovation and finest methods fosters a culture of constant renovation. By cultivating a skilled labor force, companies can adjust to transforming market needs and preserve their one-upmanship. Eventually, a holistic strategy that incorporates devices, service, modern technology, and workforce growth placements companies for continual success in the packaging industry.
Verdict
In conclusion, specialist product packaging tools service plays an essential duty in ensuring smooth procedures within production environments. By focusing on these solutions, companies can achieve optimal operational performance and extend the life-span of their machinery.
Report this page